In the truck repair business, getting the job done means having the necessary parts on hand. But inefficient inventory practices can hold your shop back, causing unexpected costs and frustrations. That's why you need a powerful partner like Easy Truck Shop, with our truck parts inventory software designed to streamline your operation and boost your bottom line.
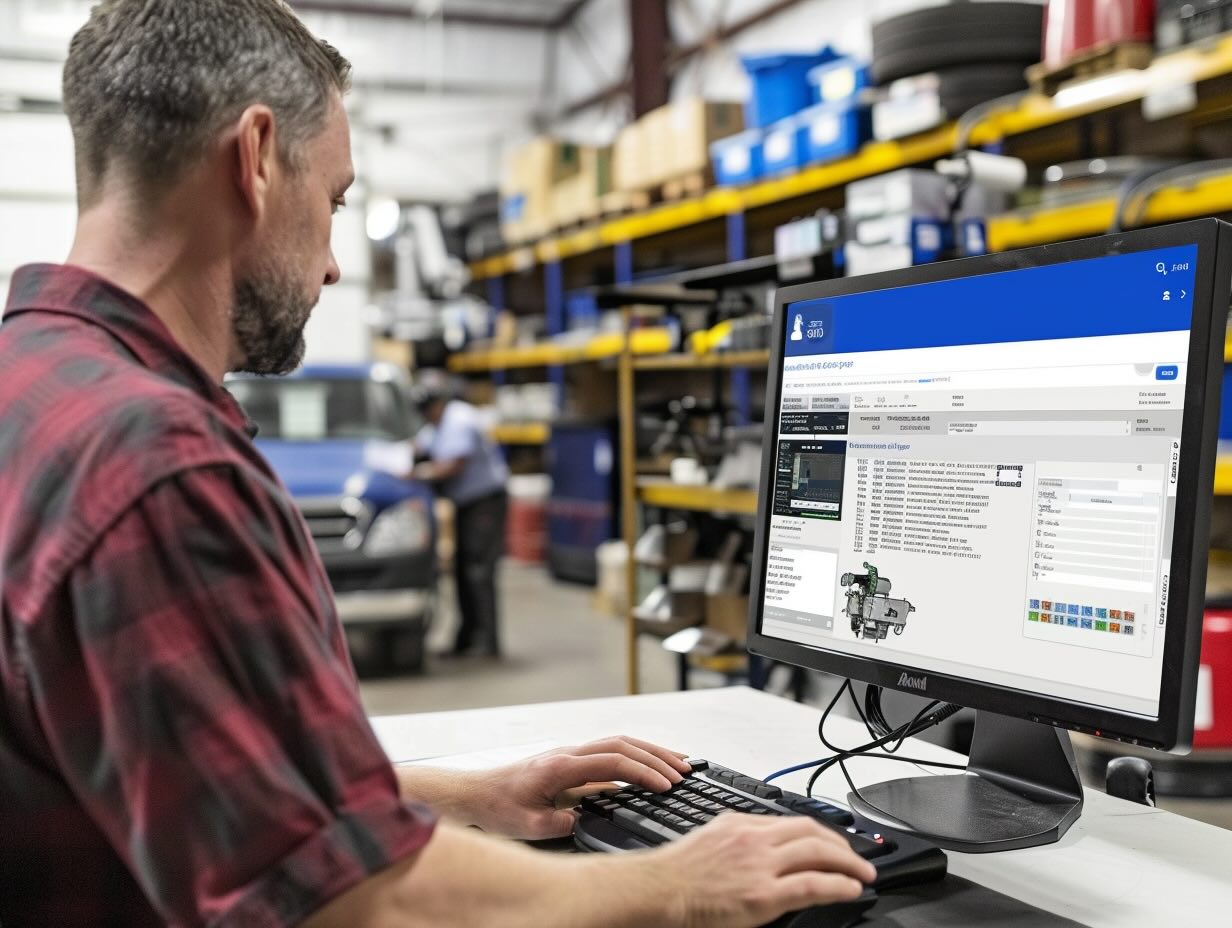
Hidden Costs of Excess Inventory
While some costs of excess inventory are obvious (like the money tied up in those parts), many truck repair shops fail to see the full financial impact.
- Capital tied up in stock: Overspending on unnecessary parts limits your shop's ability to invest elsewhere.
- Wasted storage space: Could that prime real estate be more effectively utilized with a streamlined inventory?
- Obsolescence and dead stock: In the truck repair industry, parts evolve. Old inventory risks becoming a financial burden.
- Inefficient labor use: Chaotic inventory areas waste mechanic time they could be spending on billable work.
Paying the Price for Part Shortages
Stock-outs aren't just a headache – they have a tangible financial cost. When you're missing crucial parts, it's not just your efficiency that suffers.
- Disruptive downtime: Trucks off the road equal lost revenue. Each missing part delays customer vehicles and hurts income.
- Rush orders and higher costs: Emergency orders with expensive shipping fees eat into your profit margins.
- Disgruntled customers and damaged reputation: Delays test customer loyalty and can hurt your shop's reputation.
- Missed business opportunities: Turning away work due to parts unavailability caps your growth potential.
Easy Truck Shop: Your Solution for Efficient Inventory Management
Easy Truck Shop's software transforms your inventory management. Outdated spreadsheets and manual processes are replaced with:
- Precision stock tracking: Real-time visibility into part quantities prevents overstocking or running low.
- Optimized ordering with reorder points: Software assists in setting appropriate reorder levels for your specific needs.
- Streamlined organization: Implement barcode scanning, bin locations, and other systems for efficient parts retrieval.
- Valuable insights: Track your inventory turnover, identify slow-movers, and make data-supported decisions.
- Supplier management: Software lets you track order history and performance by supplier, helping you make better choices.
Stop letting inefficient inventory management hinder your success. Discover the power of Easy Truck Shop's truck parts inventory software and see the difference it makes for your shop. Book your personalized demo today and take the first step towards greater efficiency and profitability!
Related Articles
Discover more articles on related topics to expand your knowledge.
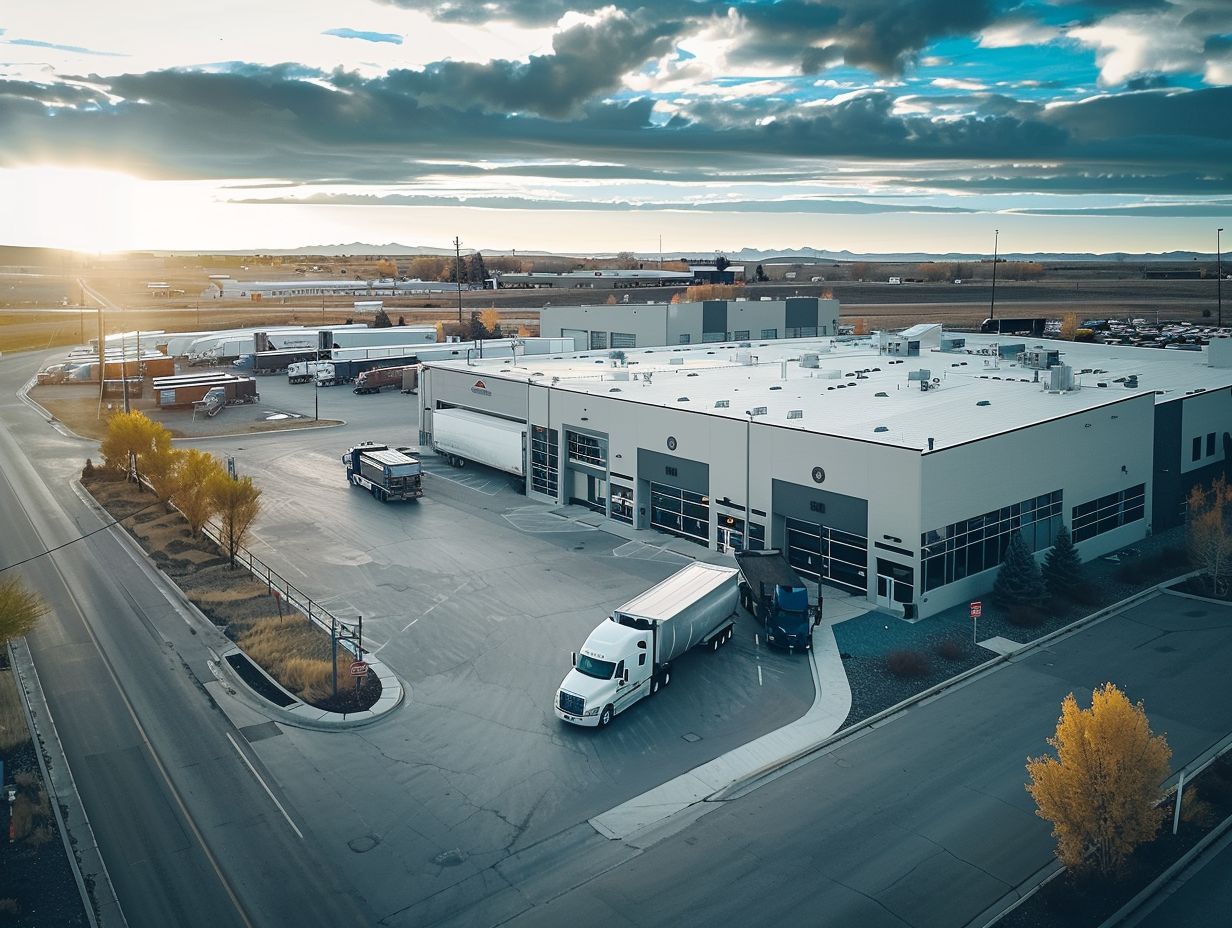
21 Pro Tips on How to Run a Successful Mechanic Shop
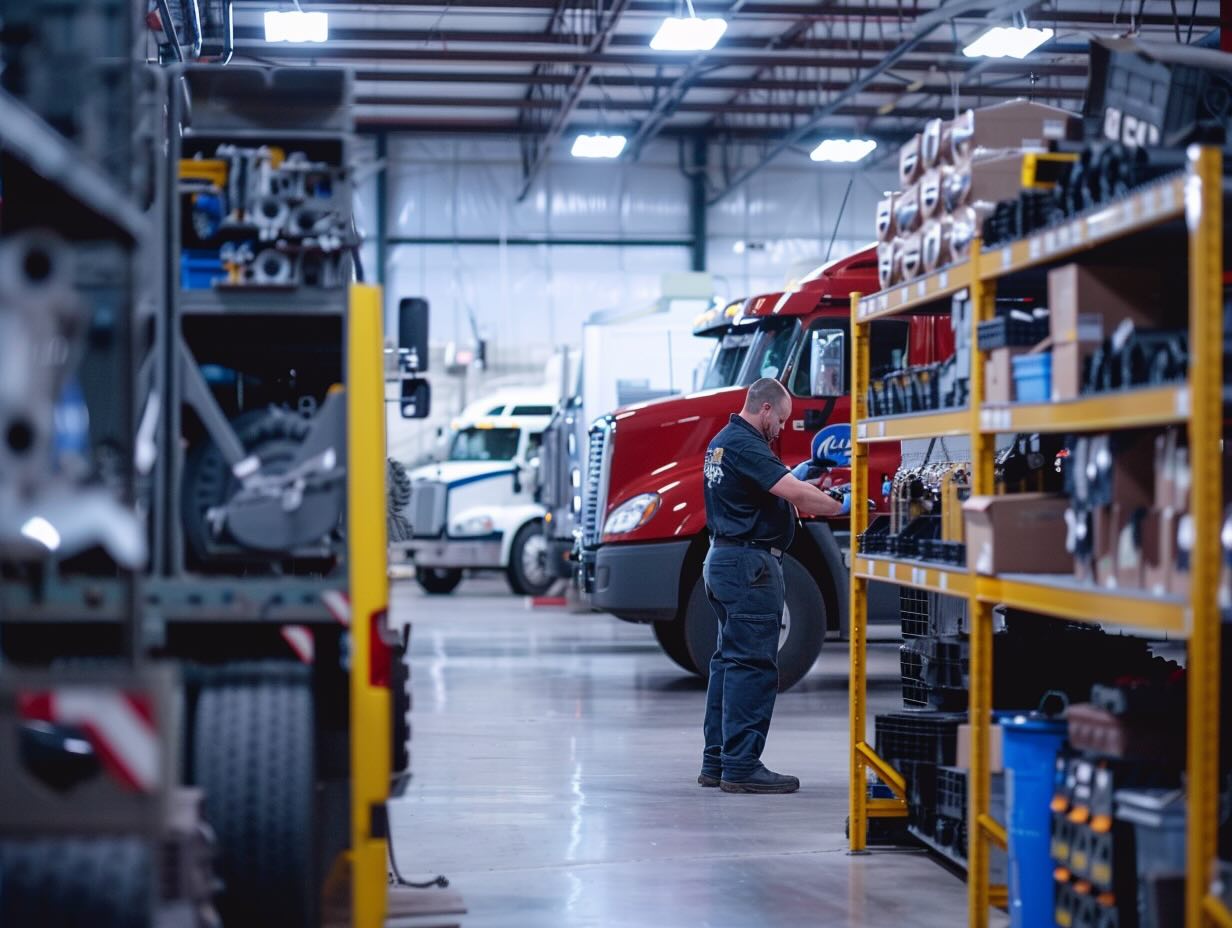
Parts Inventory Management Software For Repair Shops
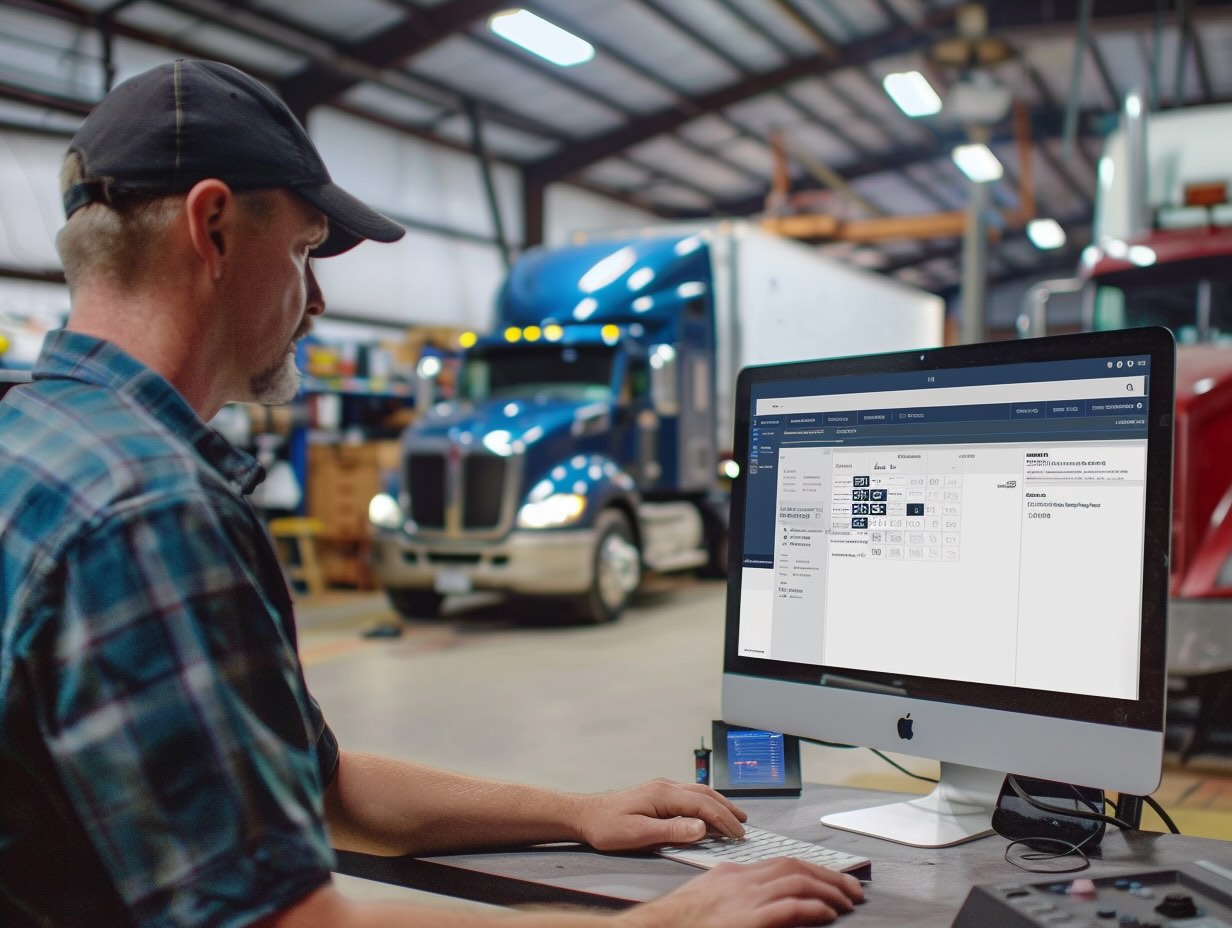